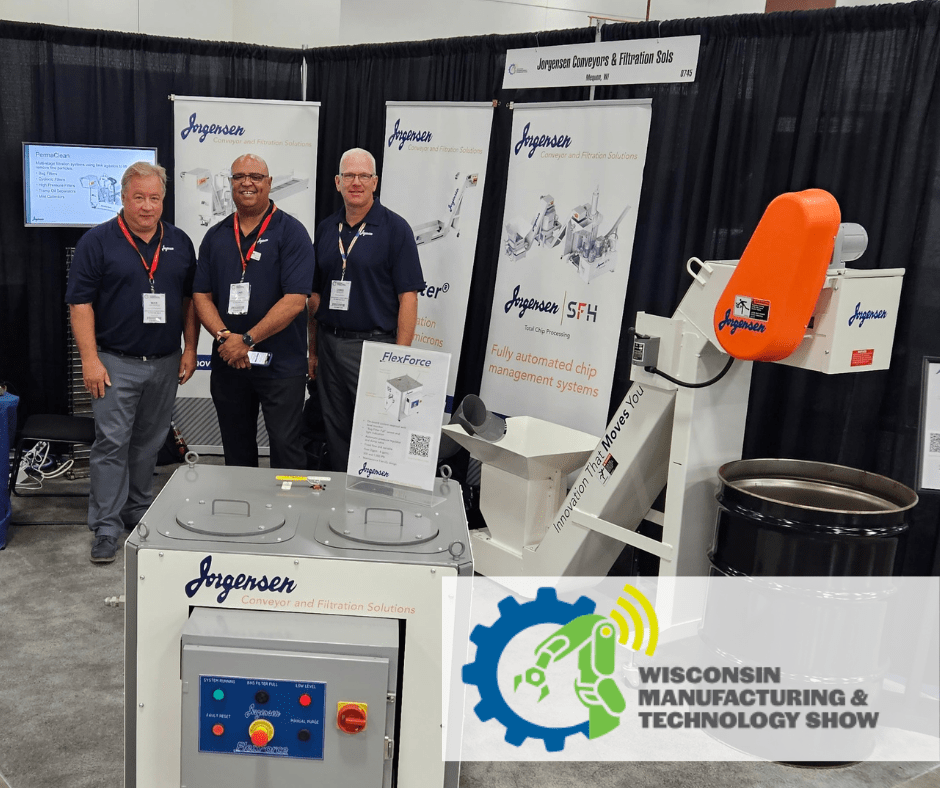
Jorgensen Shines National Spotlight on New Conveyor, Filtration and Coolant Solutions in Midwest
November 6, 2023 10:37 amJorgensen Conveyor and Filtration Systems showcased several conveyor, filtration and coolant system solutions on the national level in early October with two stops at major manufacturing shows. Visitors to the Wisconsin Manufacturing & Technology Show 2023 (WIMTS) Oct. 3-5 experienced demonstrations of the company’s Will-Fill automated coolant solution, FlexForce high-pressure coolant system and Auger Assist conveyor. Jorgensen also featured several conveyors with the enhanced, first of its kind, EcoFilter 80 filtering solution at Mazak’s DISCOVER 2023 event. DISCOVER is North America’s largest private manufacturing event that occurred Oct. 9-13 at Mazak’s National Technology Center in Florence, Kentucky.
In a partnership forged with Belgian-based Will-Fill late last year, Jorgensen provides customers a revolutionary Will-Fill add-on solution that offers trouble-free care and monitoring of metalworking emulsion. The system combines automatic measuring, filling, conditioning and reporting. Will-fill systems provide a quick ROI in applications machining high-value parts requiring a high level of precision and accuracy such as aerospace and medical industries.
WIMTS attendees watched the Will-Fill system, linked to a high-performance control unit, regulate machining fluid level and condition automatically. Alternatively, Will-Fill can alert operators via Wi-Fi capability when attention is required. The system easily adapts to Jorgensen’s robust line of filtration systems or retrofits onto customers’ existing coolant systems.
Jorgensen also featured its advanced FlexForce high-pressure coolant system with variable flow rates from two to eight gallons per minute (GPM). The variable flow rate options for the high-performance through-spindle coolant system (TSC) adapt easily to a variety of applications to provide safe and efficient operation. A maintenance-friendly design incorporates an oil sight glass and oil drain chute and requires no partial disassembly for oil changes. The system’s small footprint easily integrates with existing coolant systems. FlexForce’s plug-and-play design allows it to be readily interchanged with the industry’s standard high-pressure units. Unlike industry equivalent high-pressure systems with piston pumps and inconsistent pressure output, FlexForce uses Hydra-Cell diaphragm pumps as a standard feature for virtually pulse-free operation.
The standard eight-GPM flow rate and variable flow rate options are available in 500 or 1,000 PSI configurations. They are and designed to break through the heat-generated vapor barrier created at the cutting tool and workpiece interface that causes surface deformities and tool damage. Because FlexForce gets coolant directly to the cutting zone, it improves lubrication and heat dissipation as well as cutting speeds and feeds, chip control and part surface finishes. Standard units filter to 10 microns, with additional filtration options available upon request.
At WIMTS, shops with machine tools that utilize augers to discharge chips discovered how Jorgensen’s Auger Assist Conveyor increases production by enabling machines to handle higher chip volumes. As a result, the Auger Assist’s 48-inch discharge height allows for the use of larger collection bins, greatly reducing labor needed for chip hopper management. Seven inches of discharge height adjustment provide the flexibility to adapt to many different machine tool models. Additionally, the Auger Assist’s chute is adjustable in 90-degree increments and can be arranged in three possible positions to accommodate any plant layout requirement. The unit features a coolant collection area and a drain plug to reclaim coolant. It can be used as a stand-alone solution or as the first step in an entire chip processing system.
The following week, Jorgensen joined Mazak for its immensely popular DISCOVER 2023 where visitors from across North America gathered to see the latest advancements in machine tool technology and automation. In addition to displaying conveyors on several Mazak INTEGREX and Ez Series machines, Jorgensen highlighted its enhanced industry-leading, two-stage chip removal and coolant filtration EcoFilter® conveyor. The new EcoFilter 80 features an advanced filter box configuration that enables efficient filtration of fine chips to 80-micron nominal. The EcoFilter 80 is the first economical non-drum style conveyor below 100-micron filtration.
EcoFilter® conveyors use a two-stage chip removal and filtration process that carries out large chips on a hinged or scraper belt. Fine chips flow with used coolant between the belt runs to a flow-through EcoFilter® cell where they are separated from the coolant. Clean coolant is discharged to the coolant tank while filtered fines are brushed from the filter screen and flow to the bottom of the conveyor and out the discharge.
By dramatically reducing the number of chips that migrate to a machine tool coolant tank, the amount of downtime for tank cleaning and maintenance is significantly reduced while improving pump, tooling and coolant life. The EcoFilter® is environmentally friendly, uses no consumables, and the single-drive design reduces energy consumption. As a result, shops gain increased production and profitability. Jorgensen custom engineers EcoFilter® conveyors for a variety of lengths, widths, heights and incline angles. Additionally, current EcoFilter-ready conveyors can be considered for an EcoFilter® 80 field retrofit.
Categorised in: Company News, Events, In the Press
Comments are closed here.