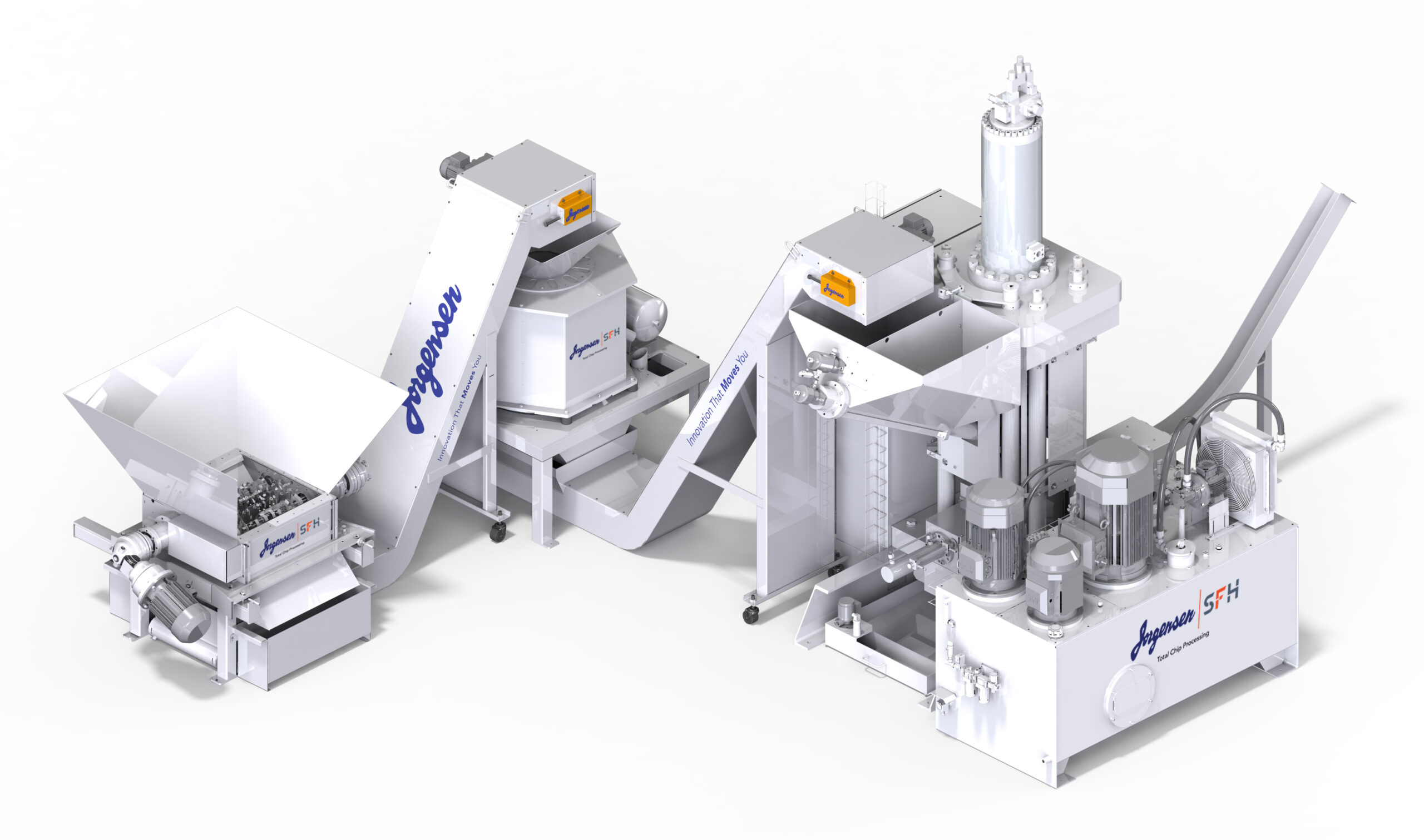
Achieving Quick ROI Through Chip Processing
March 11, 2024 4:53 pmChip Processing for Metal Machining
For optimized metal machining, shops need chip processing systems designed to meet their individual needs. Each application is unique, although most systems must handle some combination of shredding, wringing and briquetting. Complete processing with standalone or fully integrated systems that shred, wring and briquette manufacturing byproducts can reduce chip volumes by up to 90%, cut pickup and transportation costs, reclaim coolant and raise recycling values significantly.
ROI: The Bottom Line
Each system makes a targeted contribution, especially to applications that involve oil, titanium, other costly alloys, and some aluminums. The four shop scenarios below demonstrate how quickly a properly designed complete chip treatment system can pay for itself.
Stamping
A stamping facility that worked with 375 tons of aluminum each year implemented shredding, wringing, and briquetting. The resulting chip-volume reduction cut waste transport costs while coolant removal increased scrap resale value. With these savings, the processing system paid for itself in two years.
Machining and Turning – Titanium
To increase scrap resale value, a manufacturer that machined and turned 95 tons of titanium annually chose a shredding and wringing process. The company’s post-treatment scrap price rose 269%, and the system paid for itself in seven months.
Machining and Turning – Aluminum
Another shop with an annual machining and turning volume of 130 tons of aluminum looked to increase its scrap value, reclaim coolant for reuse, and simplify overall scrap handling. With shredding and wringing, scrap value rose by 129%, enabling the system to reach ROI in eight years.
Oil Reclamation
A facility that processed aluminum, titanium, brass, and copper added a shredding and wringing solution with a bin tilter. With the sole goal of oil reclamation, the system achieved ROI in 1.1 years.
As these examples show, complete chip processing increases efficiency, improves recycling values, reclaims coolant, and eliminates unproductive manual intervention. With a properly designed and configured system, manufacturers reduce chip volumes and increase their profits.
Categorised in: Case Stories
Comments are closed here.