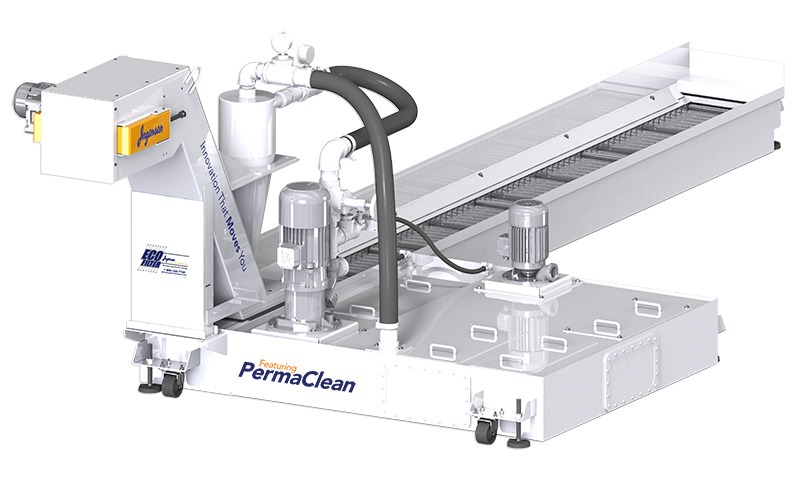
Choosing the Right System for Maintenance-Free Machining
December 10, 2024 10:12 amLabor shortages can leave shops scrambling to meet tight deadlines and deliver products on time. Upgrading to the right conveyor, tank, and filtration systems can significantly reduce manual labor for operators and your maintenance team, improving overall efficiency.
The Right Conveyor and Features
Standard conveyors that come with your machine tools are often generic, chosen for their low cost rather than optimal performance. However, a properly specified conveyor and belt with built-in primary filtration can drastically reduce operational and maintenance hours. While upgrading may involve a slight increase in upfront cost, the return on investment (ROI) is quickly realized through improved efficiency and reduced downtime.
Clean Coolant Solutions
Coolant tank cleaning is a dirty, time-consuming task many would prefer to avoid. Sludge buildup, tramp oil, and metal particles not only reduce machining efficiency but also contaminate cutting fluids and encourage bacterial growth. These issues shorten fluid life and negatively impact the health of both machines and employees.
FlexFiltration systems filter coolant down to 10 microns, making them ideal for through-spindle coolant applications by effectively removing contaminants that cause tool wear and compromise surface finishes. PermaClean systems use multi-stage filtration to maintain coolant clarity, reducing or even eliminating the need for manual tank cleanouts. FlexFiltration and PermaClean users report significant reductions in yearly tank cleaning hours, with some entirely eliminating this maintenance task.
System Controls
Conveyor automation through advanced controls ensures your conveyor is running at the right speeds when you need them most. Jorgensen conveyors communicate directly with your machine to turn on and off as needed. If a takeaway conveyor becomes overwhelmed with metal chips, UVS Ecologic Control automatically reverses then continues to clear away tough loads.
Specified Components
Lastly, end users see a dramatic decrease in labor hours by simply choosing the right conveyor features for the machining application. When a machine’s application changes, it may require different features such as X-treme duty belting, perforated apron plates, or coolant filtration.
Contact a Jorgensen expert to see which options fit best with your machining operations.
Categorised in: Promotions, Uncategorized
Comments are closed here.